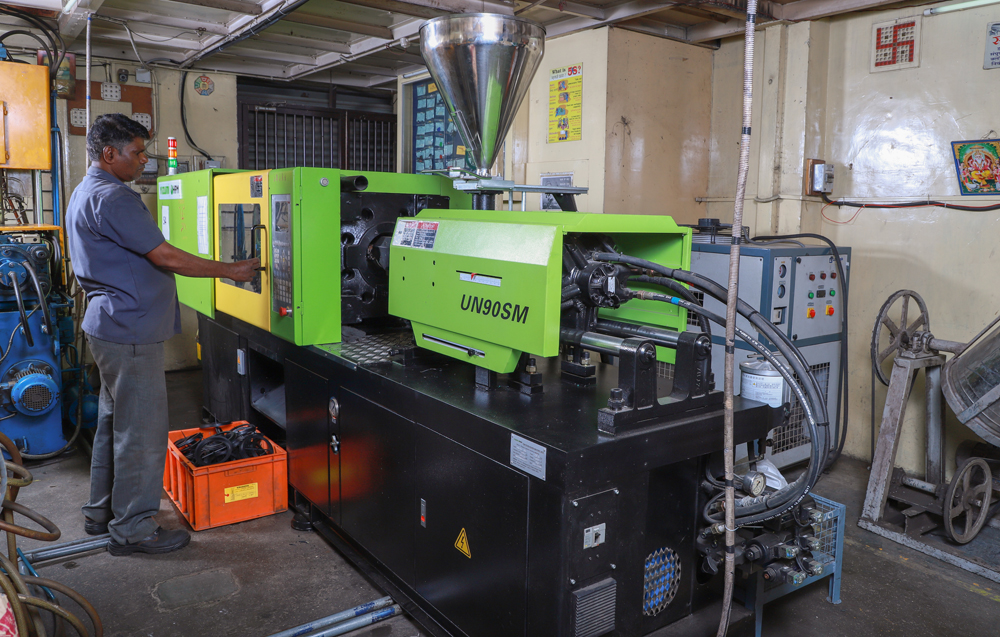
Horizontal Fully Automatic Screw type Injection moulding Machines with Servo System Micro Processor Based Control Panel
- Make Yizumi
- Clamping Force 90T
What is Injection Moulding?
Melted material is injected into a mold during the injection moulding process to produce intricate and exact shapes.This process is widely utilized in many different industries to produce plastic components. Vikas Industries, one of the top injection moulding companies in India, uses cutting edge technology to guarantee that every product we produce is precisely and consistently created.
The Advantages of Injection Moulding.
Injection moulding is a popular choice among businesses due to its rapid and efficient manufacturing of huge volumes of products. In contrast to other manufacturing techniques, injection moulding enables the quick and waste-free creation of identical parts. For businesses trying to satisfy rising demand while keeping prices down, this efficiency is crucial. Being a reputable brand among Indian injection moulding businesses, we guarantee that our procedures optimize output without compromising on quality.
Our Services at Vikas Industries
At Vikas Industries, we offer a comprehensive range of services tailored to meet the needs of our diverse clientele. As a leading choice among injection moulding companies in India, we specialize in:
- Custom Injection Moulding: We are aware that each client has particular needs. With the help of our custom injection moulding services, you can realize your unique ideas and make sure the finished items are exactly what you had in mind.
- Prototype Development: We offer prototype development services before starting large-scale production. This vital stage enables customers to test and improve their designs, guaranteeing that the finished product satisfies all requirements.
- Rapid Production: Our highly skilled personnel and state-of-the-art machinery allow us to deliver manufacturing capabilities quickly. We are one of the more adaptable injection moulding companies in India since we can manage both big orders and smaller quantities.
- Quality Assurance:One of the main pillars of our business is quality control. At each stage of the production process, we carry out thorough inspections to make sure our products live up to international quality requirements.
Industries We Serve
Serving a diverse range of industries with pride, Vikas Industries demonstrates our experience as one of the leading injection moulding companies in India. Among our clientele are:
- Automotive: We manufacture high-performance parts that adhere to strict automobile specifications.
- Consumer Goods: We offer a range of products that improve daily living, from domestic goods to electronic casings.
- Medical Devices:Medical equipment manufacturers choose us because of our dedication to accuracy and security.
Vikas Industries stands out among Indian injection moulding companies due to its commitment to quality and client satisfaction. Our skilled staff works directly with customers, including washer manufacturers in India, to comprehend their unique requirements in order to provide solutions that not only meet but also beyond their expectations. With our clients, we aim to build enduring relationships built on mutual respect and success.
Injection Moulding Process And Companies in India:Vikas Industries
One of the top companies in India for plastic molding is Vikas Industries. Our specialty is offering excellent plastic molding solutions that are customized to satisfy the wide range of demands of our customers. Being among the most respected plastic moulding businesses in India, we guarantee goods that surpass industry standards thanks to our experience and dedication to quality. Vikas Industries stands out as your reliable partner whether you need high-precision components or customized moulding services. Examine our products to see why we are the go-to option in the demanding plastic molding industry.
1. Set up the Mould
- Clean the mould device to expel shape assurance.
- Clear the apparatus vents to forestall gassing issues.
- Guarantee that the apparatus is reasonably greased up to work.
2. Prepare the material
- Issue the required measure of thermoplastic material to finish the generation run.
- Expel dampness from the material in a devoted dryer in accordance with preparing parameters when required.
- Blend the material with master batch to accomplish the required shading (If the material is exacerbated to the completed shading this isn't important).
3. Set up process
- Brace the form instrument in the press.
- Design the discharge arrangement of the form instrument in the trim machine.
- Set the guide procedure parameters including temperature control.
- Get ready working zone with extra subordinate gear as required.
- This may incorporate transport lines, accumulation boxes, apparatus protecting, work seats and so forth.
- Load the thermoplastic granules in to the feeder container.
- Improve the settings to accomplish an item to meet desires.
4. The injection moulding process
- The readied thermoplastic is filled the Hopper.
- The material channels down into the screw which is warmed to soften the plastic.
- The barrel is warmed at organized temperatures along its length (approx. 5 zones) to enable the material to cement and to move along the screw.
- The screw turns which propels the material with the weight and speed resolved to fill the depression proficiently.
- At the point when the material leaves the spout toward the finish of the barrel it is infused into the feed channels of the shape instrument.
- The feed channels enable this material to stream away from any confining influence pit of the shape device which frames the state of the completed item.
- The shape instrument is held at a steady temperature to permit simplicity of material stream and to likewise draw out the warmth from the item after infusion, in this way, the material embarks to a strong frame.
- After a foreordained cooling time the form apparatus is opened when the moving platen conveying the discharge half is withdrawn.
- The form device opens with the item held in the launch half of the instrument.
- The discharge framework at that point pushes ahead to discharge the item from the shape instrument.
- The item is accumulated in the gathering box after the cycle is finished or the parts can be picked from the apparatus as required.
Offering creative and superior plastic molding solutions for a range of sectors, Vikas Industry stands out among the leading plastic molding companies in India. We can produce precise, long-lasting plastic components that satisfy the highest standards thanks to our cutting-edge facilities and sophisticated molding procedures.We serve a variety of industries, including consumer goods, electronics, and the automotive sector, with output ranging from small to large, guaranteeing fast delivery and consistent quality.
After the formed parts are created they will be expelled from the machine territory. Every so often components will require extra post shaping work to accomplish the last completed part before being complete pressed in line with the predefined prerequisites.
Apart from our proficiency in plastic molding, Vikas Industry is renowned as one of the top manufacturers in India of MBBR Media.We manufacture effective MBBR (Moving Bed Biofilm Reactor) media, which are intended to improve wastewater management systems' biological treatment procedure. Our MBBR media offers efficient and long-lasting water treatment solutions since it is designed for maximal surface area and biofilm formation.
Additionally, Vikas Industry, which offers a large selection of high-performance washers, has built a solid reputation as a reliable washer manufacturers in India.Our washers are made to endure tough industrial uses and come in a range of sizes and materials to satisfy our customers' requirements.
At Vikas Industry, we are committed to delivering quality, reliability, and innovation across all our products and services.