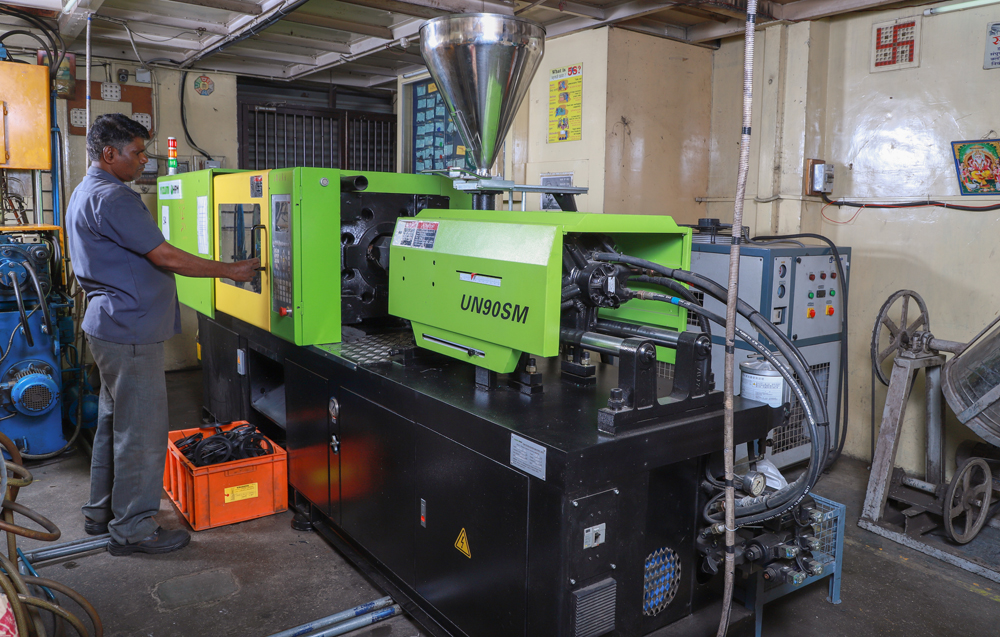
Horizontal Fully Automatic Screw type Injection Molding Machines with Servo System Micro Processor Based Control Panel
- Make Yizumi
- Clamping Force 90T
Injection Moulding Process
1. Set up the Mould
- Clean the mould device to expel shape assurance.
- Clear the apparatus vents to forestall gassing issues.
- Guarantee that the apparatus is reasonably greased up to work.
2. Prepare the material
- Issue the required measure of thermoplastic material to finish the generation run.
- Expel dampness from the material in a devoted dryer in accordance with preparing parameters when required.
- Blend the material with master batch to accomplish the required shading (If the material is exacerbated to the completed shading this isn't important).
3. Set up process
- Brace the form instrument in the press.
- Design the discharge arrangement of the form instrument in the trim machine.
- Set the guide procedure parameters including temperature control.
- Get ready working zone with extra subordinate gear as required.
- This may incorporate transport lines, accumulation boxes, apparatus protecting, work seats and so forth.
- Load the thermoplastic granules in to the feeder container.
- Improve the settings to accomplish an item to meet desires.
4. The injection moulding process
- The readied thermoplastic is filled the Hopper.
- The material channels down into the screw which is warmed to soften the plastic.
- The barrel is warmed at organized temperatures along its length (approx. 5 zones) to enable the material to cement and to move along the screw.
- The screw turns which propels the material with the weight and speed resolved to fill the depression proficiently.
- At the point when the material leaves the spout toward the finish of the barrel it is infused into the feed channels of the shape instrument.
- The feed channels enable this material to stream away from any confining influence pit of the shape device which frames the state of the completed item.
- The shape instrument is held at a steady temperature to permit simplicity of material stream and to likewise draw out the warmth from the item after infusion, in this way, the material embarks to a strong frame.
- After a foreordained cooling time the form apparatus is opened when the moving platen conveying the discharge half is withdrawn.
- The form device opens with the item held in the launch half of the instrument.
- The discharge framework at that point pushes ahead to discharge the item from the shape instrument.
- The item is accumulated in the gathering box after the cycle is finished or the parts can be picked from the apparatus as required.
After the formed parts are created they will be expelled from the machine territory. Every so often components will require extra post shaping work to accomplish the last completed part before being complete pressed in line with the predefined prerequisites.